UNIDADES DE
ALBAÑILERIA
INTRODUCCIÓN:
Son las siguientes: ladrillo de arcilla,
bloqueo o ladrilla silito calcáreo y bloque de concreto. Las unidades de albañilería pueden ser
sólidas, huecas o tubulares. Todas las unidades de albañilería no
deberán de tener ningún defecto en caso de las de concreto, deberán tener una
edad mínima de 28 días antes de ser usadas.
Mano de obra:
Las personas encargadas de la mano de obra deben ser
personas capaces y calificadas.
Exigencias:
Los muros, se construyan a plomo y en línea.
Todas las juntas, horizontales y verticales deben de estar llenos de mortero.
El espesor de mortero debe ser mínimo de 10mm. Las unidades de albañilería
deben de asentarse con las unidades limpias. No se asiente más de 1.20m de
altura de muro en una jornada de trabajo. La albañilería armada, reforzada
con acero, debe de quedar lleno de mortero.
ADOBE:
Es un material de
construcción hecho con arena, arcilla y agua, y, a veces con fibra o material
orgánico como paja, ramas o estiércol. Es moldeado en forma de ladrillo y se
deja secar al sol. El adobe es conocido por ser un material antiguo capaz de
hacer estructuras muy duraderas. Hasta el día de hoy se han preservado
construcciones realizadas con ese material, que se encuentran entre las más
antiguas del planeta. A veces se hace distinción entre los adobes pequeños, del
tamaño de un ladrillo común, y los grandes adobones que pueden llegar a medir 2
metros de largo.
La mezcla se moldea con un
marco, que luego es retirado, y se deja secar al sol por 25 o 30 días. El
tamaño generalmente, es de 6x15x30 cm, aunque se considera un tamaño aceptable,
cualquiera que pueda ser manejado con una sola mano. Sin embargo, se prefiere
un ladrillo con más espesor por su capacidad térmica.
El adobe tiene la
característica de que puede ser moldeado en casi cualquier forma y tamaño,
dependiendo de cómo se presione la mezcla. Para los ladrillos más grandes, el
adobe puede ir reforzado con paja, estiércol, cemento, barras de acero o madera.
Antes de usar la mezcla, se realiza una prueba en un frasco con agua. Se vierte
un poco de la mezcla y se combina con el agua hasta que queda casi totalmente
saturada. El frasco se sella y luego se agita vigorosamente. Después se deja
reposar. Si se acumula sedimento en el fondo, significa que hay suficiente
arcilla y es una mezcla buena para el adobe. Si la mezcla permanece líquida,
significa que hay poca arcilla y podría resultar en débiles ladrillos.
Una característica
importante del adobe es su capacidad termal. En un edificio hecho de adobe, se
regula la temperatura interna, permitiendo que en verano se conserve el frescor
y en invierno, el calor. Otra ventaja, es que es un material muy fácil de
utilizar. Entre sus desventajas, está su debilidad ante los temblores y
terremotos. Esa debilidad ha causado muchas pérdidas humanas y también
económicas, culturales y patrimoniales. Se le ha reemplazado con materiales
como bloque, ladrillos y hormigón. En países como Colombia y Perú se está
trabajando para realizar piezas de adobe resistentes a los movimientos
telúricos, ya que con otros materiales, que además son más caros, se pierde la
capacidad termal que proporciona el adobe.
ADOBE ESTABILIZADO:
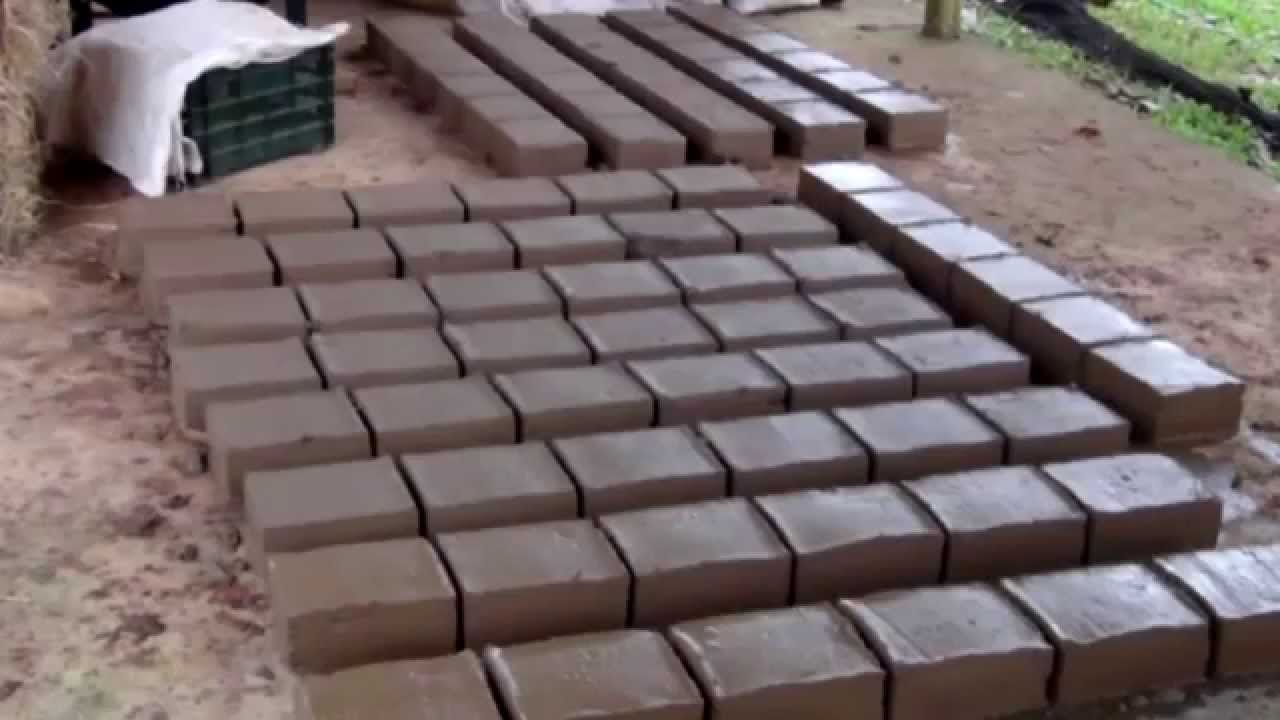
LA PIEDRA:
Se puede utilizar directamente sin
tratar, o como materia prima para crear otros materiales. Entre los tipos de
piedra más empleados en construcción destacan:
Granito: tradicionalmente usado en toda clase de muros y edificaciones, actualmente
se usa principalmente en suelos (en forma de losas), aplacados y
encimeras. De esta piedra suele fabricarse el:
Mármol: piedra muy apreciada por su estética, se emplea en revestimientos. En
forma de losa o baldosa.
Arenisca: piedra compuesta de arena cementada, ha sido un popular material de
construcción desde la antigüedad.
La piedra en forma de guijarros redondeados se utiliza
como acabado protector en algunas cubiertas planas, y como pavimento en
exteriores. También es parte constitutiva del hormigón.
Mediante la pulverización y tratamiento de distintos
tipos de piedra se obtiene la materia prima para fabricar la práctica totalidad
de los conglomerantes utilizados
en construcción:

ELEMENTOS
DE LA CONSTRUCCIÓN EN PIEDRA:
La construcción en piedra puede emplearse para muros, caminería,
techumbres, etc.
Muros: la principal
dificultad de esta construcción en piedra, es la irregularidad de la forma de
las mismas. Estas construcciones son habituales en el medio rural, y se
realizan con materiales del lugar. En la actualidad se construyen para fines
decorativos. Las piedras deben seleccionarse pues presentan variedad de tamaños
y formas, por lo cual deben ser talladas en ocasiones, para que se acerquen a
la forma prismática. Para la construcción en piedra de muros, se coloca en cada
metro, una piedra rectangular del ancho del muro, como guía de alineamiento. A
partir de allí, se apilan las piedras, recubriéndolas con mortero. Los espacios
grandes entre piedras, se rellenan con piedritas pequeñas y mortero. La
verticalidad y alineamiento deben ser muy cuidados, pues es muy fácil
perderlos. Para mantener la alineación, se coloca un tendido de cuerdas.
Caminería: la construcción en piedra de un camino, es un elemento decorativo que
brinda naturalidad y elegancia al jardín o la entrada de la vivienda.
Seleccionaremos piedras calizas o mármoles cortados en lajas de grosor medio,
como el Travertino. También pueden utilizarse basaltos, granitos, y areniscas,
y el acabado es rústico y no pulido. Estos caminos requieren de mucho tiempo
para lograr un resultado armonioso. Es recomendable seleccionar las piezas de
modo de no cortarlas. La separación entre piedra y piedra debe ser por lo menos
de 10mm. Las lajas se colocan sobre un lecho de mortero y se colocan una a una,
y se mantienen a nivel con un listón.
Arcilla no cocida:
Dentro de la
arcilla
no cocida está el Tapial, que es un muro, generalmente grueso,
levantado colocando un molde o encofrado donde se vierte barro encharcado y se
le golpea con un pisón hasta compactarlo. Es muy económico en cuanto a
materiales y energía, siendo el resultado totalmente satisfactorio respecto a
aislamiento térmico y resistencia estructural. Como en toda obra de barro, ha
de protegerse del agua por medio de recubrimientos y remates. Tiene la ventaja
de ser un magnífico aislante manteniendo una gran masa térmica y siendo
totalmente reciclable. El uso intensivo de mano de obra y la falta de costumbre
hace que actualmente su uso sea muy esporádico. El adobe es un ladrillo de
barro mezclado con paja al que se ha dado forma de paralepípedo mediante un
molde de madera y que se ha dejado secar al sol para que endurezca. La
construcción del muro se realiza por medio del aparejo de las piezas, como si
de ladrillos se tratara, aunque en vez de mortero de cemento se utiliza barro.
Arcilla
cocida:
Los
elementos obtenidos de la arcilla cocida (ladrillos,
baldosas, piezas acabado...) son materiales artificiales obtenidos de cocer
tierras arcillosas. Tienen cierto impacto ambiental por la energía consumida en
la cocción, que aunque no es muy alta, supone en conjunto valores
significativos. Son materiales inocuos y reciclables, previa trituración. Se
utilizan como áridos en rellenos, pavimentos y hormigones pobres. Como elemento
diferenciado está la arcilla expandida. Mediante un proceso de fabricación
determinado se consiguen unas pequeñas bolas de arcilla cocida muy ligeras, que
son utilizadas como árido en rellenos y hormigones (puede llegar a una
reducción del peso en un 70%). Sus propiedades resistentes y aislantes hacen de
este producto un material muy utilizado, tanto en rehabilitaciones como en obra
nueva. Es un material químicamente neutro, que no desprende gases ni malos
olores, totalmente inocuo. No se deteriora con el paso del tiempo.
ladrillos silico calcareos:
NORMAS
TECNICAS:E070 NTP 399.602
ELEMENTOS DEL HORMIGON:
BLOQUES HUECOS DE CONCRETO PARA TECHOS ALIGERADOS: